Software Solutions
As a global leader in food processing solutions, Marel provides innovative software to maximize value creation for processors worldwide. By delivering digital products and platforms that build interconnectivity, we constantly enhance our position as the digital partner of choice for the food processing industry.
As Marel continues the journey toward the smarter factories of the future, we are focused on developing connected offerings that underpin a future of sustainable, affordable food. With digitalization at the center of our strategy, our advanced solutions are transforming food production to benefit food processors, consumers and the environment.
Our world is becoming increasingly complex, and processors are looking for software and automated solutions to remain market competitive. We understand the challenges our customers and end consumers face, and create holistic solutions that address these issues, delivering value for a more balanced supply chain.
By integrating software into processing lines, we are increasing throughput and improving yield, product quality and safety. This not only improves performance and uptime but also ensures more predictable service, enables our customers to surpass sustainability and traceability requirements, and helps address the growing need for end-product flexibility.
Smarter factories of the future
The factory of the future will be a dynamic and adaptive space, built to evolve with continuously changing needs and improve food processing at every stage. To support this evolution, we have established four interconnected foundations: standardization, connectivity, security within the changing IT landscape and line management.
Four key software foundations for innovative solutions
Foundation 1: Standardization
Standardization finds simple solutions to complex problems through data collection, collation and analysis. It is the core foundation for creating a fully flexible, upgradeable, evolvable manufacturing and execution system (MES) solution and enables continuous delivery of innovative features, processes and synchronized rollouts.
Many process flaws are difficult to spot unless there are sufficient examples. Studying data reveals patterns for evaluating the suitability and workability of fundamental problems in a standardized way. At Marel, this translates to developing standard workflow processes through data modeling.
Food processing facilities can be divided into individual workflow processes that cover logistics for receiving and primary, secondary and final goods. Workflows such as ‘Start stock take’ and ‘Calculate yield’ interact with common functionalities like orders, tracking and tracing within the MES. Data is also shared with business processes such as resource planning for inventory management. The integration of workflows and MES ensures our customers are using best practices.
Marel has been collecting data from all software installations currently in operation, with a focus on secondary processing. As patterns emerge, they guide our process experts to build workflow solutions to benefit all our customers. During site visits, technicians collect post-install workflow data and install updated workflows. We are working toward workflow data being collected and implemented via the Marel Cloud, to offer processors even faster improvements.
Breakdown of the benefits
Deployment: Standardized workflows act as building blocks when constructing new systems. Processors can choose from a library of workflows that best suit their processing line, making deployment easier and more efficient. As IT landscapes continue to change, our standardized models will enable easy movement through the new environments.
Quality: As connected installations increase and more data is collected, the library will evolve. Workflows can be streamlined and flaws removed. Marel customers will benefit from new or updated workflows deployed remotely to all sites.
Knowledge transfer: Workflows can be synchronized across multiple sites, improving systems and standardizing workforce training. Specific rule changes to workflows can be made if individual site needs differ.
Easier purchasing: By standardizing sales material, processors reduce design time and are able to supply consumers with easyto- understand product information, thereby enhancing their brand recognition.
Foundation 2: Connectivity
Marel’s digital journey is constantly evolving to help processors navigate the increasing complexity of operations and maintenance. Designed to enhance digital connectivity, our program of integrated software solutions encompasses hardware, software and services to offer holistic solutions. We are transforming solutions to create a world where data and insight make food processing less dependent on manual labor. By connecting equipment, software and services, our solutions optimize processes and increase uptime.
Cloud connectivity is becoming a standard feature of Marel equipment. By connecting to the Marel Cloud, real-time and historical data is stored in customer-specific databases, providing accurate insights into machine health and performance from both technical and production standpoints. An accompanying application, available on any device, grants access to data and actionable insights, making it easy for processors to operate and maintain their equipment with a user-friendly dashboard.
Dashboards are integrated into all connected products and serve as a powerful tool for data visualization. They present the data collected for traceability and real-time monitoring of key performance indicators such as yield, throughput, capacity and labor efficiency. This allows processors to make immediate datadriven decisions that improve their line efficiency and ultimately increase profitability.
As data is stored on the Marel Cloud, customers can allow our service and support teams instant access to information that will supply an immediate, clear understanding of any issues. This way, more problems can be solved remotely, shortening resolution times. If a service specialist needs to visit the site, they can be better prepared with the right parts or materials.
Where we are on the connected journey
Our first connectivity offering is SmartBase, an advanced solution for monitoring machine health. The program is in the early stages of rollout in Northern Europe and North America, with plans for expansion into other regions soon. Seven solutions now come with SmartBase as standard, and retrofitting for customers’ installed base is also available. Today, we have more than 200 solutions in the field operating with SmartBase.
Our SensorX and FleXicut solutions were the first to be onboarded to SmartBase. In 2022, we made SmartBase connectivity a standard feature of five more solutions: the ModularOven, I-Slice, Compact Grader, Nuova-i and Marel Spectra. A further 25 solutions are road-mapped for inclusion in 2023.
Foundation 3: Security within the changing IT landscape
Moving to cloud computing offers many advantages, including improved service and maintenance, faster equipment updates, data loss prevention and scalable flexibility. By using cloud-based software, processors can lower costs as they only pay for what they use, rather than expensive licensing fees for software that quickly becomes outdated. With the Marel Cloud, software is always the latest version and adapts as a business changes.
One of the greatest benefits of Marel Cloud technology is its advanced security, which is constantly updated through a larger cloud provider in addition to Marel’s own stringent security measures. Connecting to the cloud also enhances the security of Marel’s overall IT landscape, moving away from hierarchical data architectures to data ecosystems that enable more aggregate data relationships.
With data becoming a primary driver to running an efficient processing business, we are acutely aware of the importance of understanding cyber-security risks. We are dedicated to delivering trustworthy and resilient digital solutions and services to our customers.
Marel digital solutions are built with security as a top priority. SmartBase operates within a protective cloud environment to keep customer systems and data secure at all times. Customers retain ownership and control of their data, granting access to Marel for remote support only.
Development with a security focus: ISO 27001 certification
To ensure that Marel consistently follows best practices in data protection and cyber resilience, we are in the process of acquiring ISO 27001 certification, the international standard for information security management systems. Gaining certification will build trust in our process control and demonstrate that we continuously implement and develop our security processes.
The current scope for certification is the Marel Cloud platform. An internal audit was finalized in 2022, and an external audit is planned for early 2023. Following certification of our cloud platform, we will move toward certification of all platform layers.
Integrating security by investing in people and processes
Security goes hand in hand with standardization. By reducing the number of variables in a system, we can increase the trustworthiness of our software and make it easier to protect data. This can be achieved by standardizing our development and deployment processes, such as hiring the right people to develop new tools and training our teams to implement them effectively.
Over the past few years, we have been systematically standardizing our development processes, building up the necessary competencies to support connectivity.
Foundation 4: Line management
The food industry faces the immense challenge of reducing reliance on skilled labor in secondary and further processing, while also delivering a growing variety of end-products to meet customer demand. Line management is key to delivering the right products at the right time. Integrating software into line equipment, implementing factory-wide MES software, and automating lines decreases labor dependency and increases product flexibility.
In February 2022, Marel initiated a program to address industry trends and challenges. The program focuses on balancing automation and flexibility through integrated and connected line solutions in secondary processing. In this way, it aims to accelerate key developments, increase automation and adapt Marel’s portfolio to standard interfaces.
Our roadmap to advance secondary processing includes innovations across all Marel business segments, starting with the poultry portioning line and beef steak line.
In the industry in general, current secondary processing lines are made up of standalone equipment with varying technologies and frameworks. This means that effective line operation is reliant on a skilled labor force and has limited flexibility, with slow product changeovers.
The program for integrated line solutions addresses these issues by standardizing Marel equipment both mechanically and electronically and by designing for modularity and flexibility. Central Line Management allows for machine-to-machine communication, standard connections between Marel and third-party equipment, and software integration for a connected facility. This reduces operator dependency, improving processing efficiency and ease of use.
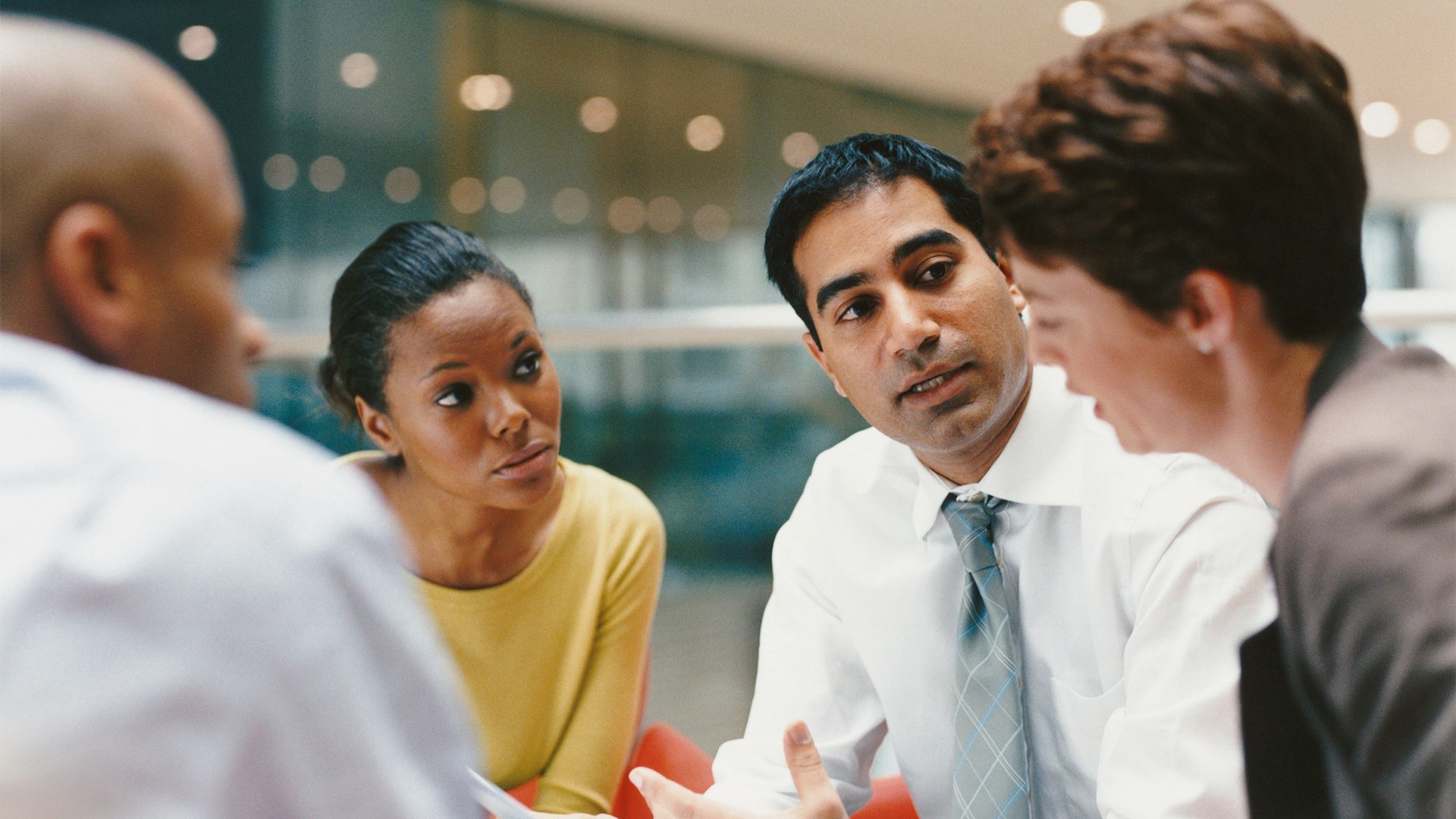
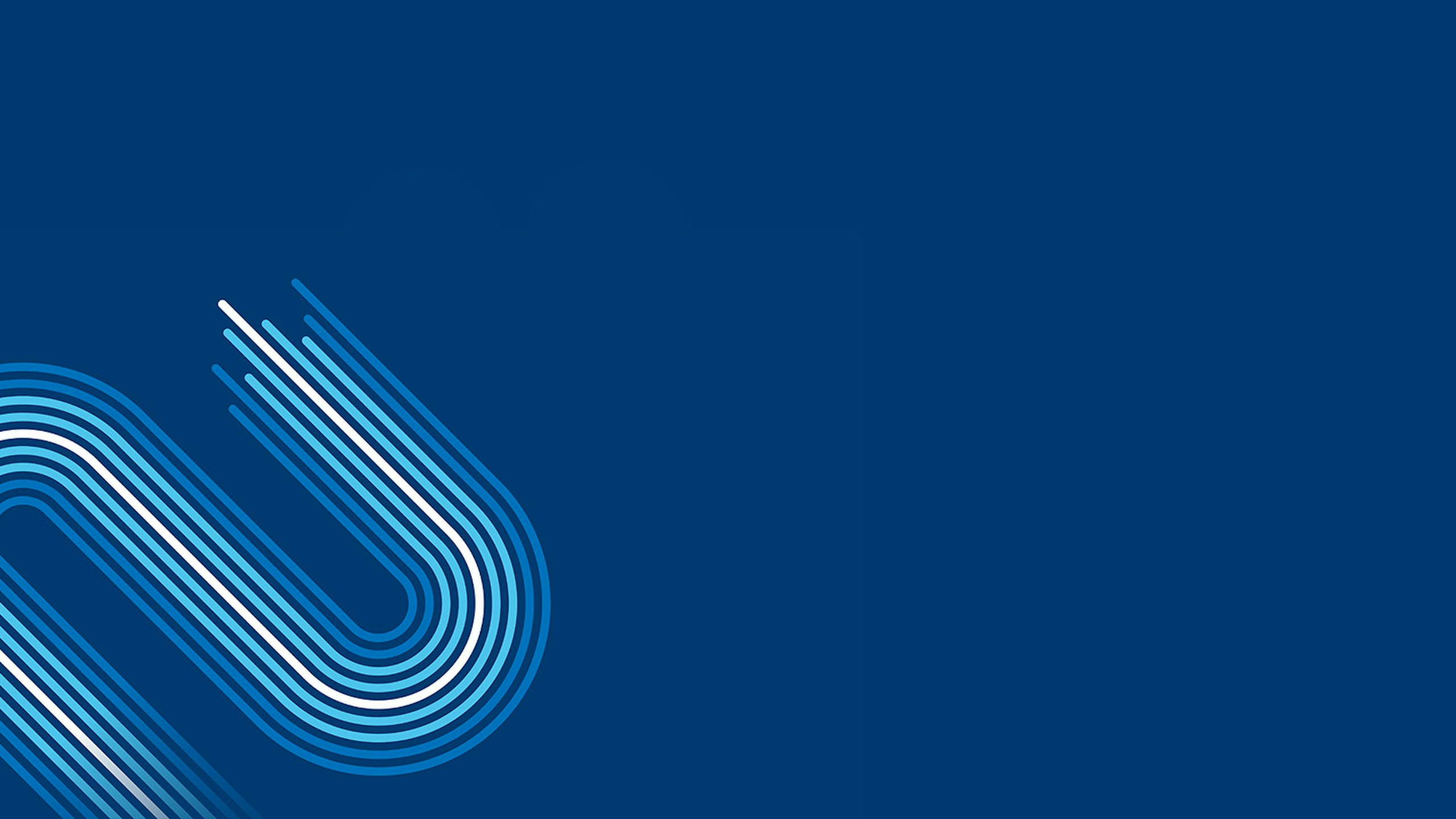
Customer story:
Master Good masters the primary process with IMPAQT
Master Good is a forward-thinking poultry enterprise in Hungary that processes about 260,000 birds per day, working in two shifts, six days a week. The primary processing line runs at a speed of 15,000 birds per hour (250 birds per minute), which makes it impossible for the human eye to measure efficiency. However, by implementing the intelligent IMPAQT software from Marel, Master Good has seen significant improvements in its primary process.
IMPAQT software has reduced product losses by shifting equipment performance from the subjectivity of guesswork to objective data, based on interval and overall production. Data shows where product losses occur in real time, allowing Master Good’s staff to quickly identify and address the root causes.
Timeline
Industry drivers for software solutions
During the pandemic, Marel has seen similar market trends across all four business segments. As we move toward solutions that combine software, equipment and services in one holistic approach, we examine the market trends and digital needs of our customers.
See the detail with traceable products
Increased regulation and consumer demand for end-toend traceability and sustainability are key challenges for the food processing industry today. Our customers must comply with a growing number of laws and provide consumers with transparency regarding their products and practices.
To meet these demands, Marel’s sophisticated software enables processors to accurately capture detailed information at all stages of production. This is essential for establishing the quality, safety and provenance of end-products. Our digital traceability systems can also manage and minimize recalls, organize inventory and make meeting regulations efficient with ready access to detailed historical data.
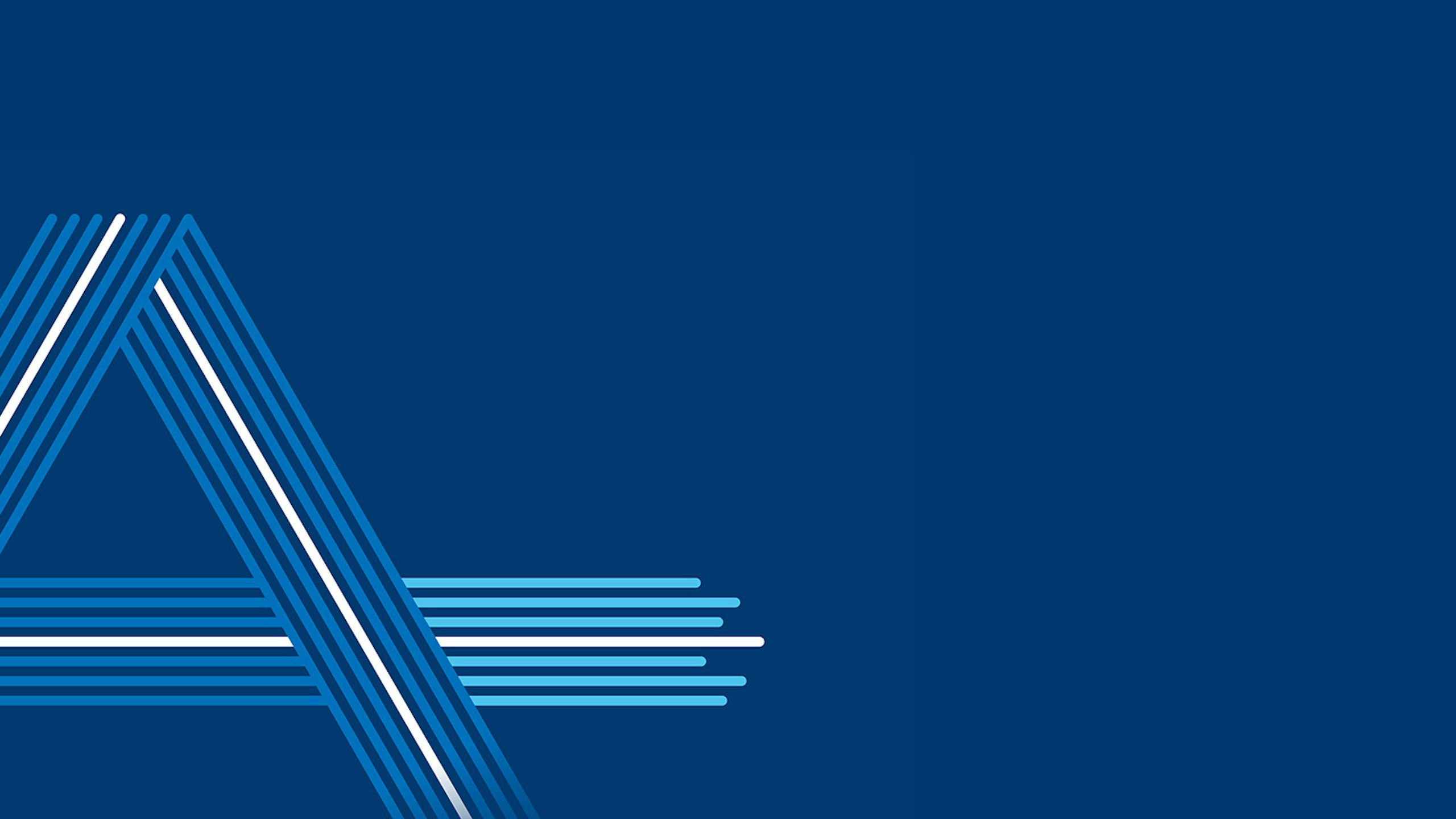
Customer story:
Sanford steps into a digitalized future
Sanford, a globally recognized fish processor with a 150-year history of operations and growth in New Zealand, has ventured into the digital world. The company’s business scope is broad, ranging from fishing vessels of various sizes to processing whitefish, salmon and other seafood.
In 2021, Sanford invested in Marel’s Innova Food Processing Software and began its journey to digitalization. With Innova’s comprehensive Manufacturing Execution System and Product Management System, Sanford can integrate all pillars, accessing accurate, real-time data from any enabled computer. The software enhances operations by providing operators and managers with greater monitoring and control over the entire process, from raw material receiving to end-product dispatch.
Since the 1990s, Sanford has been a leader in sustainable fish industries. “It is vitally important for us to have systems in place that can enable and support our decision making as we manage our processes from sea to plate,” says Andre Gargiulo, Sanford’s Chief Customer Officer. As the Innova software rollout continues, the company is poised to become even more sustainable by reducing food waste, improving yield, increasing traceability and eliminating the challenges of paper-based systems.
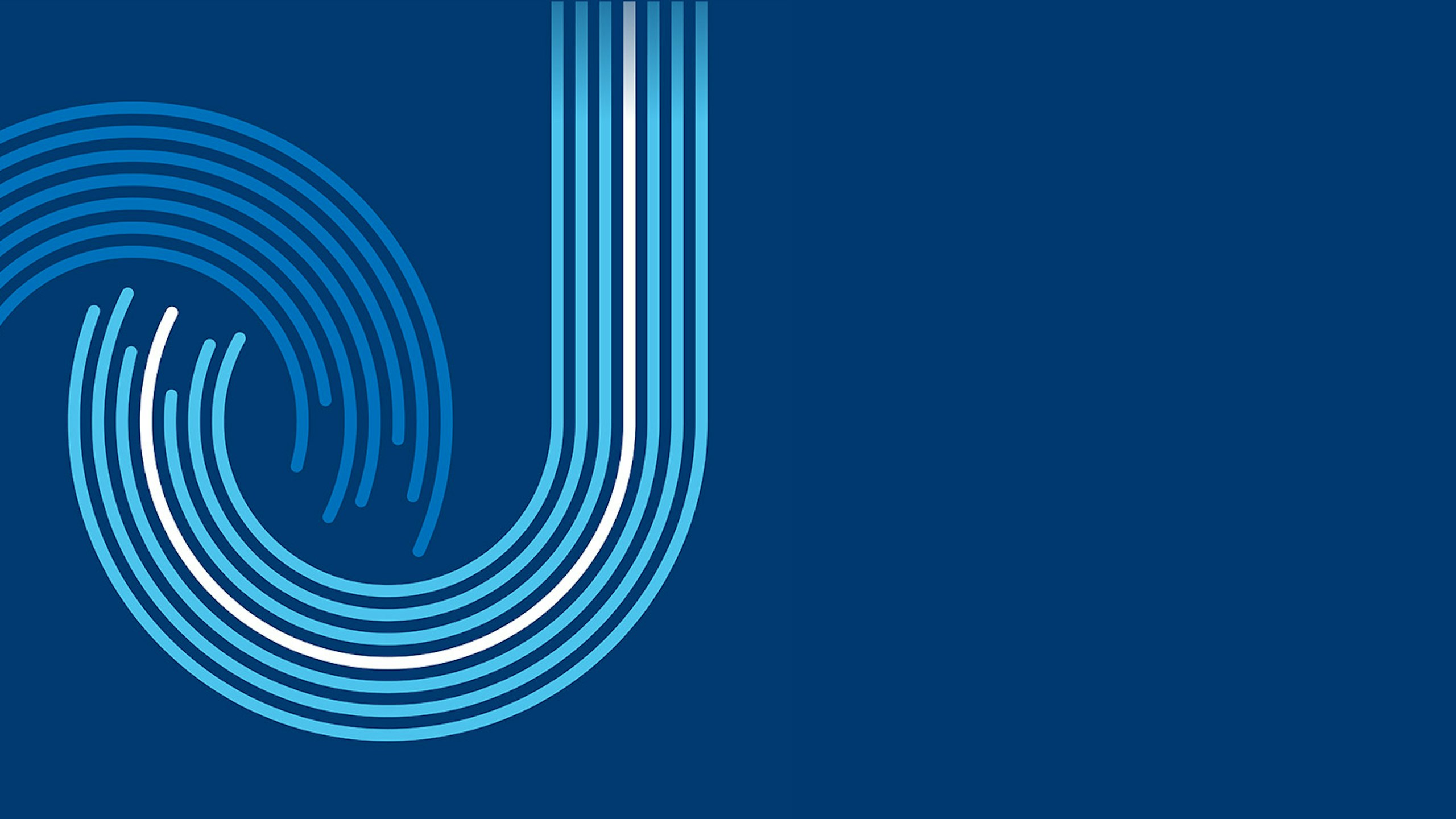
Did you know?
The future of connected cooking with SmartBase
In 2022, we launched a pilot project to evaluate the benefits of reactively monitoring a SmartBase-connected ModularOven. The ModularOven functioned correctly, with product going in and coming out cooked evenly. However, by acting on data gathered through SmartBase and communication with the operator, we were able to optimize the oven’s performance even further, resulting in a 20-40% reduction in energy use.
These exciting results yield valuable insights and data that bring Marel closer to achieving 24/7 proactive monitoring for our connected equipment. This advanced level of monitoring will not only optimize energy efficiency, but also offers insights into machine health for predictive maintenance and reduction of total ownership costs for our customers.
Software Solutions events in 2022
In 2022, we brought Marel customers together by hosting our North American and Oceanian Software KnowHow user conferences in person once again. We also celebrated the inaugural Innova Asia Roadshow, introducing our valued Asian customers to the advantages of digital innovation. These events allowed us to strengthen our customer community through active engagement and feedback.
Software KnowHow North America
In October, Marel hosted the first in-person Software KnowHow in North America since 2019. We focused on fostering customer engagement and building local software user communities. Attendees enjoyed presentations on connecting equipment to the Marel Cloud for machine health, as well as supporting MES and intelligent solutions that lay the foundations for smart factories. We also hosted product demonstrations, training sessions and security panels, and our customers shared their experiences with using Marel software and connectivity to enhance productivity, management and the power of data.