Global Supply Chain
Global Supply Chain is responsible for procurement, manufacturing and logistics within Marel. We pride ourselves on our ability to produce solutions according to our customers’ needs, delivered at the right time and right cost, all while maintaining a sustainable approach.
Our team of more than 3,400 experts, along with colleagues recently welcomed from Wenger, works to build long-standing relationships with partners, distribution networks and key suppliers.
Together, we facilitate the innovation and distribution of standalone equipment, full-line solutions and spare parts. We also support Service, which ensures that our customers are well taken care of and underpins our reputation as a trusted maintenance partner.
The year in review
Global Supply Chain had a busy and productive 2022, including a change in leadership, investments in transformative initiatives, and navigating pandemic-related challenges.
Solid performance amid shortages
Despite logistical challenges brought on by the pandemic, we achieved relatively good performance on equipment delivery in 2022. We also managed to ramp up revenues in the fourth quarter thanks to strong order intake in the first half of the year, though parts availability issues put pressure on profitability. Continuing Marel’s co-location strategy enabled us to optimize production costs. We currently have 18 manufacturing sites for equipment and spare parts that support our extensive sales and service network.
Financial initiatives
Marel made significant investments to support our goal of EUR 3 billion in revenues by 2026, with 50% coming from aftermarket services and software. These investments include transformative initiatives that support our end-to-end spare parts journey and role as a trusted maintenance partner. We are working to automate and digitalize the manufacturing platform, supply chain and aftermarket to provide the speed and scale needed to meet the financial targets for year-end 2023.
Global manufacturing platform
Investing in automation and digitalization
Cash capital expenditures, excluding research and development expenses, are projected to rise to an average of 4-5% of revenues in the period 2021-2026, before returning to more normalized levels. This increase will drive the performance improvements needed to achieve our 2023 financial targets.
The long-term outlook for the industry is unchanged, so Marel will continue to invest in digital solutions, spare parts handling and streamlining the backend. We remain focused on automating and digitalizing our manufacturing platform, supply chain and aftermarket to shorten lead times and support the 2026 target of 50% of revenues being generated by service and software. Marel’s aftermarket revenues, composed of recurring services and spare parts, have continued to grow throughout the years, reaching 40% of total revenues in 2022. Our spare parts revenues have been strong, reflecting our commitment to investing in the spare parts delivery model and shortening lead times.
New distribution and manufacturing facilities
In 2022, we initiated several key investments to enhance operations and meet customers’ needs. Parts used for manufacturing and spare parts for customers run at different tempos, and we aimed to shorten lead times to customers and improve planning and optimization of parts scheduled for manufacturing activities.
One of these investments was a new, digitalized Global Distribution Center, strategically located in Eindhoven, the Netherlands. This center will become operational in 2024 and improve flow, flexibility, scale and efficiency, shortening lead times as intended.
We also invested in a new production facility next to the current operations in Nitra, Slovakia. This facility will allow us to increase production in a cost-effective location.
In addition, we are continuously digitalizing, automating and improving flow in our main poultry facility in Boxmeer, the Netherlands. Our new 10,000 m2 warehouse, known as the Farmersland project, will streamline operations by consolidating multiple small warehouses around Boxmeer into a single location close to the manufacturing halls. The warehouse will be operational in the first half of 2023.
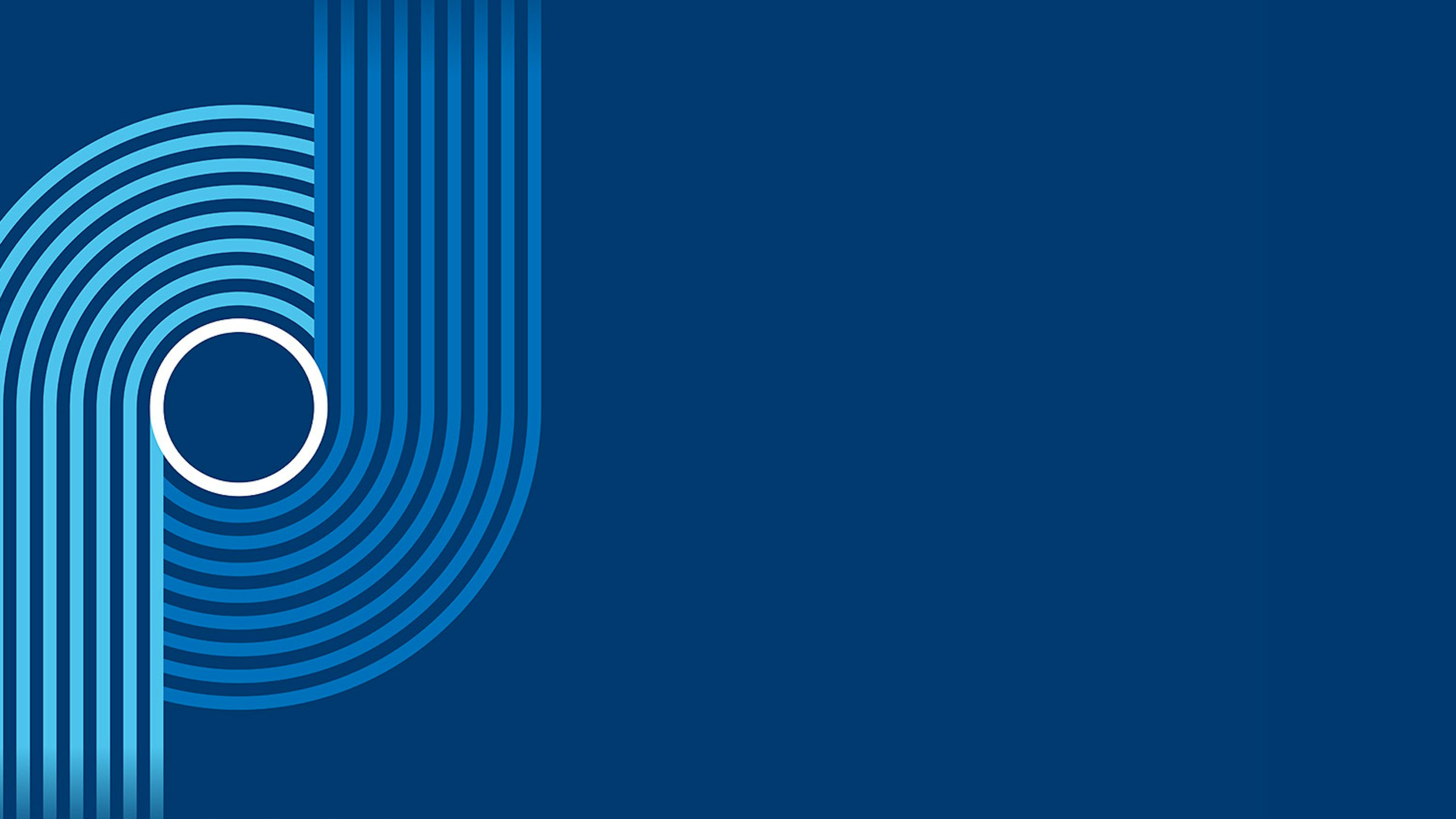
Case study:
Buford warehouse success story: 23% rise in on-time delivery
In 2020, we embarked on a journey to improve the efficiency and professionalism of our North American spare parts operation. We implemented the new spare parts operating model, and in June 2020, we split our inventories in Gainesville to regain simplicity, control and transparency over spare parts and manufacturing parts.
To further improve our response times and delivery performance, we established the Order Fulfillment Team, dedicated to spare parts handling and purchasing. Finally, in June 2022, we physically split our spare parts inventory and moved it to a separate location, the new Buford Distribution Center.
The move was a huge success, thanks to the tireless efforts of our project team, a large group of Marel volunteers and external helpers. Over the course of a weekend, they moved more than 8 million parts into the 10,000 m2 Buford warehouse. The result was a 23% improvement in on-time delivery performance, greater cost efficiency and improved work safety, all with minimal disruption. This move is a significant milestone for our company, and we are pleased with the positive impact it has had on our spare parts delivery in North America.
Balancing the load between manufacturing sites
In early 2022, COVID-19 lockdowns affected our efficiency and output performance. However, Marel’s co-location strategy enabled us to minimize the impact significantly, meaning that only a limited number of deliveries to customers were delayed.
Marel faced considerable changes in market demand and had to take extra measures to balance demand and capacity at each manufacturing site. Some sites increased capacity to maintain good delivery performance, while others decreased capacity to control costs. The manufacturing sites showed exceptional collaboration, such as taking on tasks from colleagues, traveling to other sites to provide support, and co-locating products sustainably. This demonstrates our strong unity and customer focus in the Global Supply Chain team.
We also made and implemented important co-location decisions to simplify the organization and minimize the impact of ‘mixed sites,’ where one site was supporting several business units. An example of this is the OneMeat initiative, where we have begun moving manufacturing of our meat-processing solutions from Boxmeer to Lichtenvoorde. We also plan to relocate manufacturing of our solutions for the processing of prepared foods from Støvring to Boxmeer.
Pricing
Marel maintains a global price list to administrate the sales prices in its product portfolio. In 2022, we saw high inflation for raw materials, with the cost prices increasing significantly during the first half of the year. Fortunately, in the second half of the year the price cost stabilized, primarily due to lower stainless steel prices.
To respond to fluctuations in cost, Marel has a continuous price revisions process. We begin by studying the global price list to administrate the sales prices in the product portfolio. As a response to inflation and the resulting effects on operating costs, we executed three price revisions on the global price list, including equipment, software, spare parts and hourly rates (tariffs). The process for price revision is based on the continuous development of macroeconomic trends as well as a quantitative assessment of the market environment.
In addition to price revisions, we tightened our quote validity in 2022. For equipment, the validity was reduced from 120 to 60 days, and for parts, it was reduced from 60 to 30 days.
The already enacted pricing actions and volume upside are expected to filter through until the second quarter of 2023, with variations depending on the time lag by business mix. For aftermarket, the time lag is around six to eight weeks, compared to three to six months for standard equipment and nine to 12 months for larger projects. This should support improved price/cost coverage and margin expansion toward our 2023 financial targets.
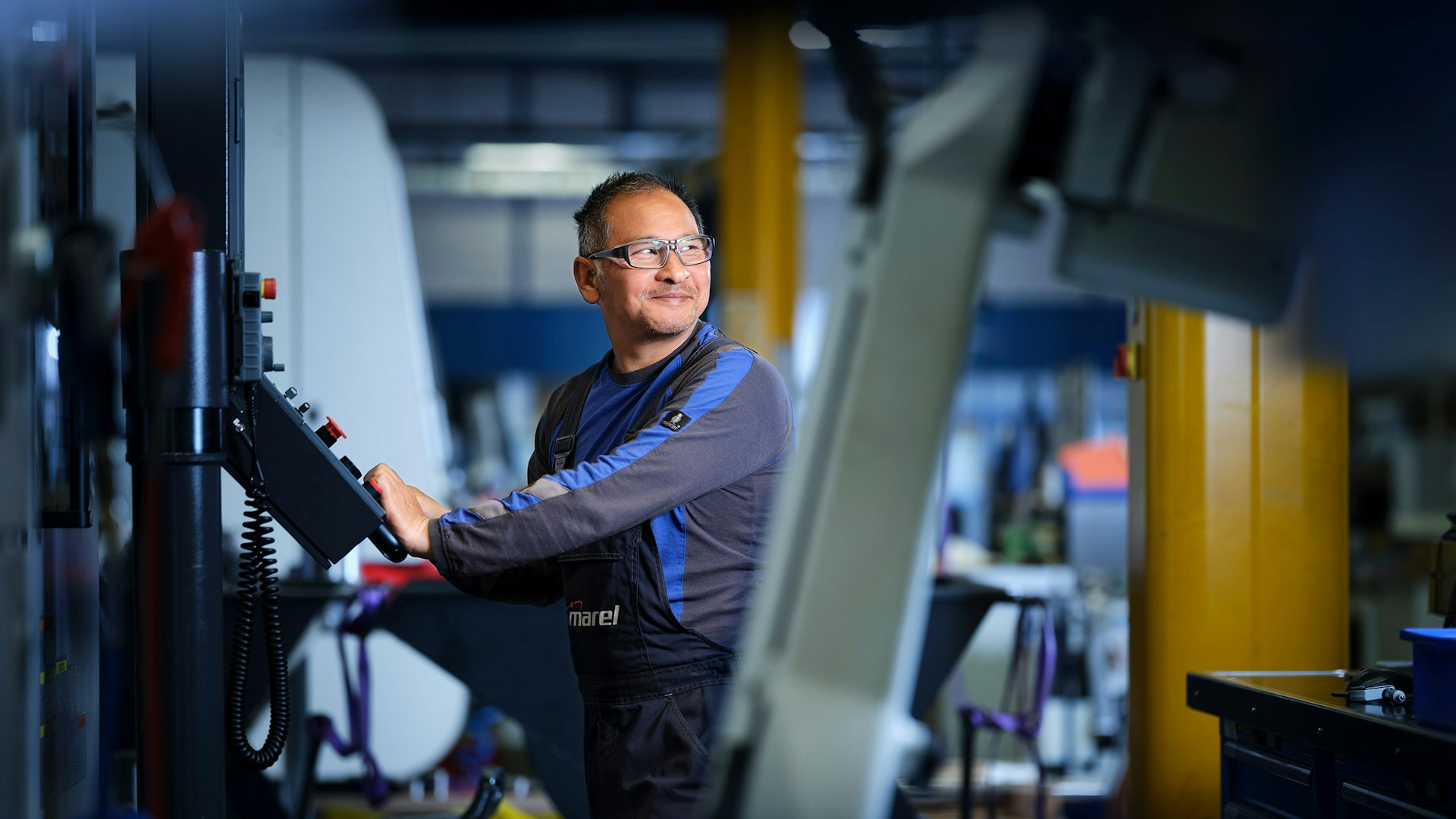
Procurement
Navigating the semiconductor crisis with Innovation and suppliers
Procurement focused on mitigating the impact of the semiconductor crisis by prioritizing parts. We achieved this through close co-operation with Marel suppliers and by actively searching for alternative components with the Innovation team. To ensure swift action for critical suppliers, we established crossfunctional focus teams. We managed to minimize the impact with several suppliers, even amid heavy supply chain disruptions.
We expect that the situation will slowly improve in 2023, but it will call for full attention from Procurement, Innovation, Manufacturing and our suppliers. We worked collaborating in different ways with our main supplier, helping them to adjust their scheduling processes and inventory strategies. This collaborative approach will be vital to addressing the ongoing challenges successfully.
Responsible sourcing team in Lodz Shared Services Center
In October 2022, Procurement installed a responsible-sourcing team in our Shared Services Center in Lodz, Poland. This team is dedicated to supporting Procurement’s sustainability goals by ensuring that suppliers comply with Marel’s Supplier Code of Conduct, as well as encouraging suppliers to join our EcoVadis initiative.
Developing procurement expertise with the Marel Procurement Academy
Procurement is all about people, and to develop the capabilities of the Procurement team, we launched the Marel Procurement Academy.
The first courses took place in 2022, including:
- Foundation course focusing on strategy and planning
- Basic legal training for strategic purchases
- Advanced negotiations training for all Procurement staff
- Strategic sourcing training focusing on creating category strategies
Building on the first year’s success, the Marel Procurement Academy will continue in 2023 with an emphasis on supply chain management and supplier relationship management courses. Participants can also fulfill additional requirements, such as joining Marel’s sustainability journey.
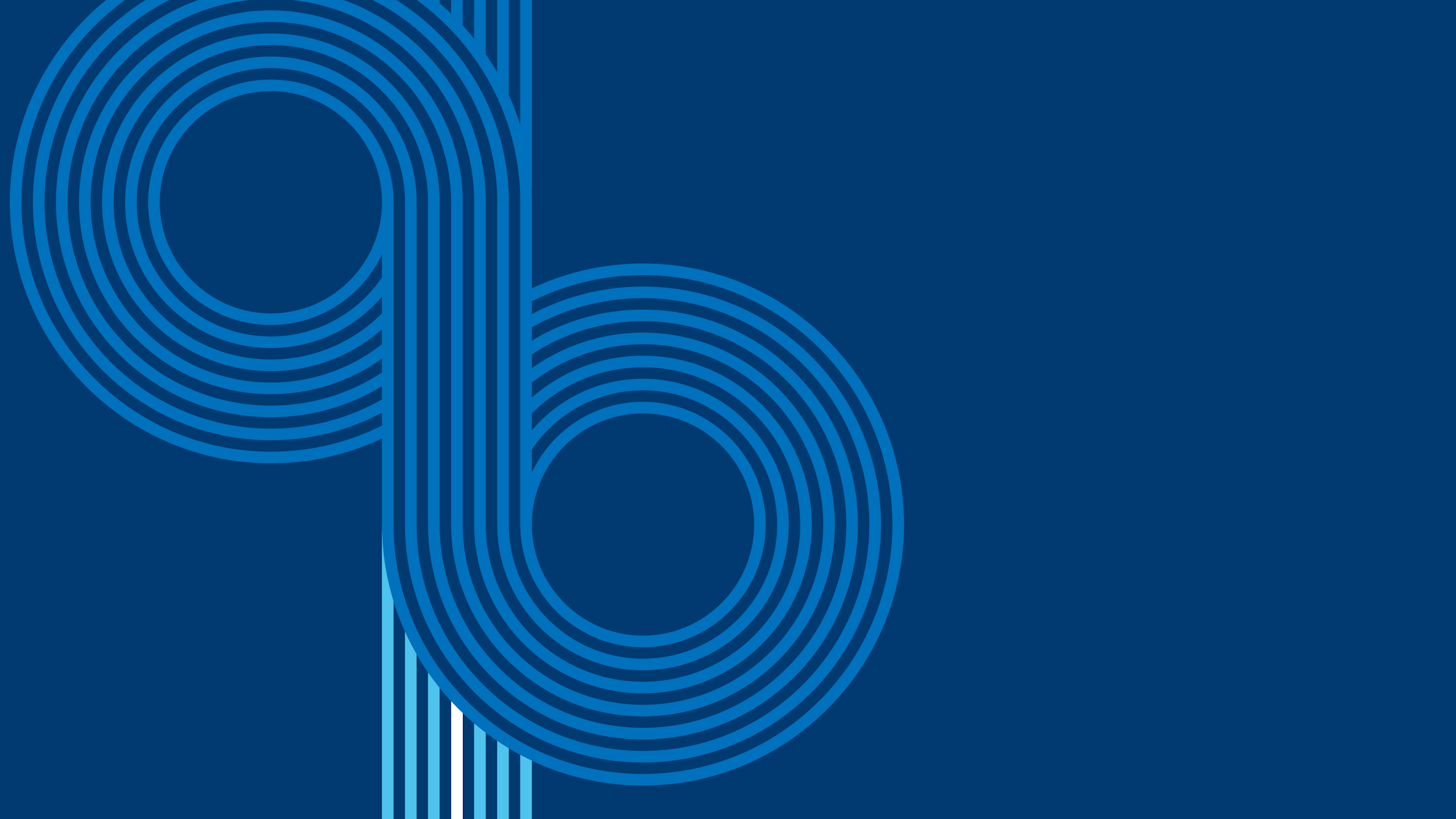
Case study:
Breaking ground at the Global Distribution Center in Eindhoven
Taking the next step on our spare parts journey, we have commenced construction of our new state-of-the-art Global Distribution Center, strategically located in Eindhoven in the Netherlands. With a 13,875 m2 warehouse, the new and digitalized distribution center will eventually house and distribute Marel’s full range of spare parts, primarily to customers in Europe, the Middle East and Africa. It will also replenish local Marel inventories close to customers in Asia and Oceania, China, North America and Latin America. Our objective is to solidify our role as a reliable maintenance partner and ensure consistent lead times for our customers in all regions.
The strategic location will offer the latest possible cut-off times for customer orders for same-day shipment. The center will be operated on the new SAP S/4HANA enterprise resource planning (ERP) software platform with the extended Warehouse Management System (eWMS) and a highly automated AutoStore solution. The Global Distribution Center will be fully operational by the second quarter of 2024.
New production facility purchased in Nitra
In the third quarter of 2022, Marel invested in a new production facility adjacent to its current operations in Nitra, Slovakia. We made this strategically important investment to improve production efficiency and cost-effectiveness.
The 18,700 m2 facility is named Nitra West and officially opened in November. We have already transferred warehouse operations into the new building. Equipment assembly commenced in January 2023 following the completion of minor interior building projects, and the building will be in full use in the first half of 2023.
Marel Nitra
New laser and storage tower in Nitra
In October 2022, we completed the installation of a new laser cutting system and automated storage tower for metal sheets. The use of automated storage and loading eliminates the need for manual handling of heavy stainless steel sheets, improving the ergonomics and safety of the operation. The laser was supplied by sheet metal processing company Bystronic and is the latest generation fiber type, replacing the old CO2 type. This new generation laser cutting system can cut at speeds up to five times faster on thin materials, is easier to maintain and reduces machine operating costs by 50%. The installation will ensure that we can meet the increasing demand for stainless steel parts as Nitra increases its output in 2023.
Global Logistics
We are continuously evolving our Global Logistics operations. In 2022, we initiated an important project to establish the Global Logistics organization at all Marel sites, except for Brazil and Lichtenvoorde, the Netherlands where we expect to roll out the project in 2023.
We also conducted and planned multiple tender activities, reviewing bids from suppliers offering services across different transport modes. The EU Road tender took place in 2022 and will be fully implemented in 2023.
In addition to establishing the Global Logistics organization, we made sure to implement best practices. These include the secure utilization of frame agreements and carriers we selected from the tender processes.
The Global Logistics organization spanning all Marel sites operates under guidelines that promote scalability, process alignment and knowledge sharing to ensure an efficient and consistent way of working.
Initiating a parcel tender for improved shipping efficiency
In 2022, we undertook an initiative to unify our shipping operations across all our shipping locations. Previously, these operations were managed through local account setups, but we sought to improve collaboration and efficiency by implementing a new system.
To achieve this, we initiated a parcel tender, inviting carrier companies to submit proposals for their parcel delivery services. We held sessions with carriers to explain our company and future logistics strategy, and presented our global parcel footprint. Based on the proposals received, we nominated FedEx/TNT as our primary parcel carrier, with DHL as the backup carrier.
Marel’s recent acquisitions, PMJ, Wenger and Sleegers, have also been incorporated into this framework.
Transport Management System
Our Transport Management System is an integration platform that will enable Marel to create a higher degree of integration (EDI) with strategic carriers and create an efficient pick-to-ship process through the warehouse. It is a critical middleware platform, acting as a bridge between separate software systems to facilitate communication and data exchange between them, ultimately creating a more efficient shipping process.
The Transport Management System will be used for our Global Distribution Center in Eindhoven, the Netherlands and other Marel shipping locations to enable integration and create transparency within spend and freight cost validation. The platform will ensure that track and trace links together with visibility of milestones from shipping to delivery.
Wenger acquisition creates synergies on freight spend
In 2022, Marel made a strategic move by acquiring Wenger, a global leader in pet food, plant-based protein and aqua feed processing solutions. This acquisition presents numerous opportunities for the Wenger sites to benefit from Marel’s discount structure on freight costs. Moreover, adding Wenger’s activities and locations will expand Marel’s reach and enable us to achieve even better rates going forward.
We have already made progress by implementing source technology, which has led to savings on freight costs. In 2023, other pilot Wenger sites are following suit, further streamlining operations and maximizing cost efficiencies.
Key sites had no recordable injury
We continuously strive to make working environments even safer for our employees. In 2022, we made incredible progress toward our target of zero harm, making this goal more tangible and attainable for all Marel sites.
Through proactive and preventative safety measures, we were able to decrease recordable incidents by 25% and increase hazards reported by 28% during the year. This was largely due to the constant focus and leadership of our managers, who regularly conducted ‘safety walks,’ gathered feedback from employees and acted promptly on any reported hazards.
We use our in-house Track concern management tool to record incidents and follow up on the root causes. In addition, we share lessons learned from incidents with all our colleagues in Global Supply Chain, with our operation directors leading calls twice a month to discuss safety concerns and share their insights.
These ongoing efforts have paid off, as two of Marel’s key sites, Nitra in Slovakia and Guaporé in Brazil, had zero recordable incidents throughout the year. We are very proud of this achievement and consider it a testament to our commitment to health, safety and the environment (HSE).